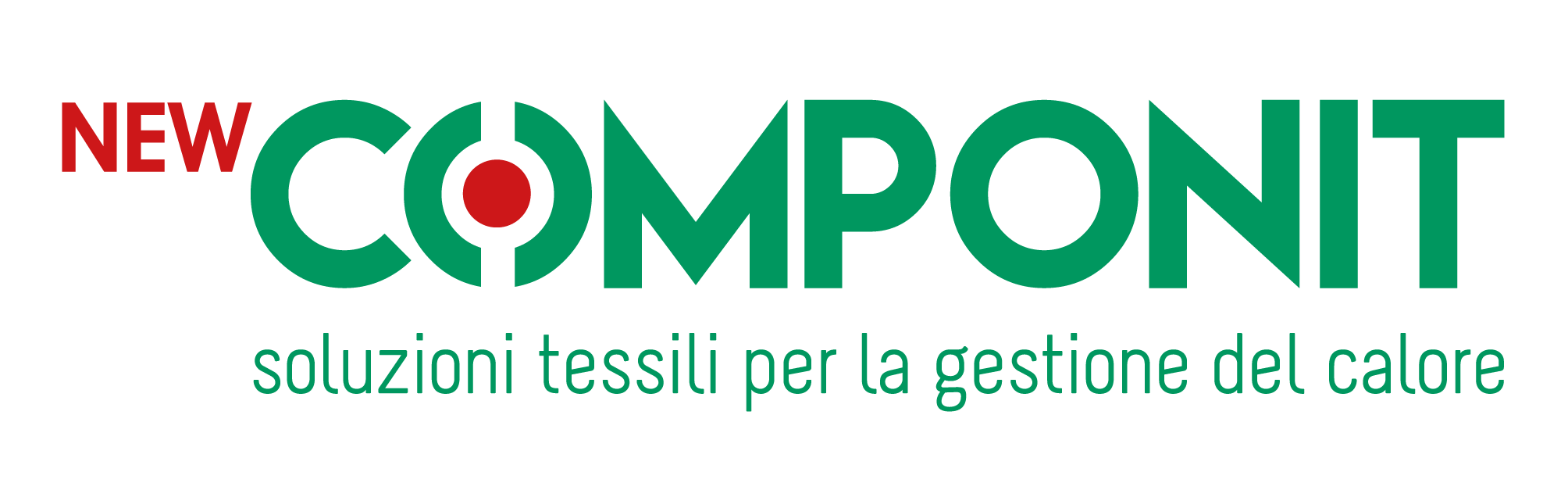
In un impianto industriale, qualsiasi sia il settore di appartenenza, possono insorgere numerosi problemi; alcuni sono all’ordine del giorno e di conseguenza le soluzioni possono essere a portata di mano.
In altri casi invece si possono verificare delle problematiche meno comuni dovute al ripetersi quotidiano di una situazione dannosa, molto più complesse da risolvere.
Questo è il caso dei materiali granulari: parliamo di quel pulviscolo, dalla granulometria più o meno elevata, che si forma durante il processo industriale e che finisce per danneggiare i macchinari.
Come spesso accade in queste situazioni, tendiamo a rimandare la risoluzione di un problema che non ci sembra imminente o le cui conseguenze non sono immediatamente visibili.
Ma è proprio in questi casi che, con il passare del tempo, si creano delle incrostazioni che rischiano di compromettere il funzionamento di caldaie industriali, silos, forni, filtri a sacco, scambiatori di calore, ventilatori industriali, scrubbers, condotti e alloggiamenti dei filtri a maniche.
I settori industriali coinvolti sono i più disparati, basti pensare a:
- il pulviscolo dell’industria della ceramica;
- le polveri d’acciaio delle fonderie o delle acciaierie;
- il gesso dell’industria del cemento;
- le sostanze polverose del settore alimentare, chimico o farmaceutico;
- le ceneri di combustione delle centrali elettriche.
Le incrostazioni che si formano sono il risultato della presenza di polveri incombuste o di polveri stoccate che, se non rimosse correttamente, tendono a solidificare rischiando di danneggiare il macchinario o comprometterne il funzionamento.
Vediamo insieme qualche esempio:
- nei ventilatori industriali l’accumulo di depositi sulle pale può sbilanciare il rotore e causare pericolose vibrazioni;
- nelle caldaie e negli scambiatori di calore i depositi di cenere possono intasare i tubi;
- nei silos i materiali rischiano di depositarsi e creare delle ostruzioni.
In tutti questi casi si pensa erroneamente che la rimozione della polvere preveda una qualche tipo di soluzione ingombrate, costosa, di difficile installazione / rimozione o, peggio ancora, che interrompa il ciclo produttivo.
New Componit ha, invece, sviluppato le trombe SAFEFON®, un sistema di pulizia acustica che, a differenza dei sistemi più tradizionali, come martelli, soffiatori d’aria e riavvolgitori meccanici, è versatile ed efficiente nella rimozione delle polveri.
Le onde sonore di bassa frequenza ed alta intensità danno vita a dalle vibrazioni interne che colpiscono i depositi residuali esercitando un effetto fluidificante. Gli impulsi sonori sono emessi da un generatore pneumatico e la loro frequenza è poi modulata da un diffusore che può avere varie forme e dimensioni a seconda dei requisiti dell’applicazione e delle esigenze di installazione.
Il sistema di pulizia sonora Safefon®:
- non provoca effetti collaterali alle strutture;
- è di facile installazione;
- funziona in maniera del tutto automatizzata;
- non prevede il fermo impianto;
- garantisce una riduzione dei costi operativi e di manutenzione.
Per avere maggiori dettagli tecnici,

Roberto Tacchinardi – Sales Manager